Philips undergoes major restructuring Company addresses operating, patient safety and quality, and supply chain challenges
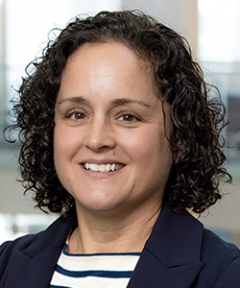
By Liz Beaulieu, Editor
Updated 10:24 AM CST, Fri February 3, 2023
AMSTERDAM – Philips has announced it will reduce its workforce by another 6,000 roles globally by 2025 in a bid to simplify its operating model.
The company plans to eliminate 3,000 roles in 2023 and the other 3,000 in 2024-25.
“This change and these reductions will help make Philips more agile, more competitive and, ultimately, result in supporting better outcomes for our customers and a simpler, more productive and more engaged workplace for employees, motivated and attracted by our purpose,” said Roy Jakobs, CEO, during a conference call to discuss the company’s fourth quarter and full year financial results. “To enable this, a renewed culture will be built at Philips, focused on our core purpose: transparency, being patient and people-centric and where we have all clear accountabilities and feel fully empowered.”
The announcement follows Philips’ decision to reduce its workforce by 4,000 roles last year. About 3,000 of those roles have already been eliminated, leaving about 1,000 still to be eliminated this year.
Unlike the previous workforce reductions, which were more “generic,” these will be more targeted, with a focus on shifting more talent and R&D dollars into the businesses themselves, Jakobs said.
“With the shift of model, we indeed take on the functions, in particular, to lean out the organization and bring more into the business, but also strengthen the regions,” he said. “And then we have a shift in innovation model that also plays a part, but that's also a big part of shift of resources more into the businesses.”
Simplifying the company’s operating model is only one of a three-pronged plan that Philips is putting in place to create value. The other two: improving patient safety and quality, and supply chain reliability.
On patient safety
Philips is taking a number of measures, including elevating leadership to the Executive Committee and holding all business leaders directly accountable for patient safety and quality within their businesses. It has also made patient safety and quality a KPI for all employees.
“Over 70% of the issues we faced in the past few years have been design-related,” said Francis Kim, head of quality. “Therefore, our primary task has been to ensure the design process is extremely robust. This means linking product development from inception with a patient view and the highest product performance requirements embedded throughout. The result will be innovative products with highest safety and efficacy.”
On supply chain reliability
Philips is making changes on three fronts: its end-to-end setup; its products and processes; and its supplier management. The company in April plans to transition to customer-centric, end-to-end supply chain teams that closely align to its different businesses, with dedicated leaders for each business, and it has already started the process of redesigning 200 electronic subsystems and printed wire boards.
“In terms of supplier management, our base has become too broad in recent years, with well over 5,000 suppliers, and has been hampered by significant decommits and visibility challenges, resulting in increased material supply risks,” said Willem Appelo, COO. “To respond to this, in the short term, we are strengthening our relationships with suppliers and driving better visibility deeper into our supply base. We are also continuing to improve resilience and reevaluating dual-sourcing initiatives. The next stage is to reduce the number of suppliers and develop long-term strategic partnerships, which we strongly believe will improve quality, consistency and delivery.”
Comments