Move lean techniques to front office
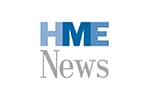
By HME News Staff
Updated Sun May 31, 2009
Despite their flexible application, lean techniques are sometimes overlooked for office operations. This may be because there is no tangible or visible product involved in office operations. The main “product” in an office setting is information. Waste in an office setting is difficult to see - it does not litter the floor like wasted material in a warehouse. Yet a typical HME front-end operation is rife with waste and workflow problems. Common forms of waste in an HME office include excessive waiting, rework loops (correcting errors), hand-offs and missing or incomplete information.
There are many factors that can contribute to waste and office overload, including too few staff and lack of training. There are also process-related issues. Here are the top five:
Lack of standard work practices
Standard work is the foundation of lean. It is defined as one of the one best ways to perform a process or task in the most effective and efficient manner possible. Standard work practices can reduce errors and improve process results, yet many offices lack them. An effective technique involves creating a standard work document that is displayed in the area where work takes place. The document must be simple - the main steps and important information should be no more than one page - and it must be very visible and easy-to-read. Standard work documents include the main process steps listed in the proper sequence, along with other key information like timing requirements. Also, they often include some type of diagram or process flow map.
Failure to effectively manage interrupts
Being constantly bombarded with questions, phone calls and e-mails can create uneven flow, as well as increase the potential for errors. In lean lingo, interrupts are known as “random arrivals” because people often react to interrupts in a random, unplanned manner. Every time there is a non-essential interruption, some type of waste is created. While it is unrealistic to expect that all interrupts can be eliminated, it is possible to gain better control over interrupts to create a smoother workflow. The first place to begin is to monitor/track all interrupts for a short period of time to identify trends and patterns. This can be accomplished using a random arrival log (who, what, when and how long). Once trends are identified, it may be possible to redesign workflow in order to address and minimize specific types of interrupts. A common form of interrupts for HME intake staff include phone calls inquiring about order status and product information/availability. Making product information available online can help to reduce product information calls.
Excessive batching and queuing
Providers typically batch paperwork at various process points. One of the keys to achieving lean flow is to minimize uneven workflow. Creating a smoother workflow can be accomplished by having smaller “piles” of work waiting to be processed. Spreading these out over a longer period of time instead of rushing to finish processing larger piles of work in a compressed timeframe can create a smoother flow of work. This is a lean concept known as batch size reduction and work-leveling. Cross-training staff will provide more flexibility and can help to maintain a more level workflow as people are moved around to cover areas with increased activity and fluctuating workloads.
Lack of visualization
Lean is about being aware of work status. The use of visual controls that allow staff and leaders to monitor the status of work can be very effective at helping to ensure employees manage their information and paperwork flow. For example, always consistently knowing how many CMNs, prescriptions and other documents are awaiting signatures and return helps sharpen people's focus and also creates a sense of heightened responsibility. Information is posted either electronically or manually for everyone to see and should be updated in as close to real-time as possible.
Lack of process-level metrics
The only way to really control and improve a process is to effectively monitor the process using relevant and meaningful metrics. Process-level metrics can serve as focus indicators to let you know when a process breaks down or becomes derailed. An example of process level metrics is the percent of initial intake forms completed and accurate, amount of documents that require rework, number of forms with missing signatures, etc.
Conclusion
Lean thinking is moving beyond the factory and warehouse floor and into more businesses and office operations. HME providers can leverage the power of lean in order to transform office operations by reducing wasteful practices and improving overall results.
- Chris Calderone is the founder of Lean Homecare Consulting Group.
Comments