Wheelchairs you want to service
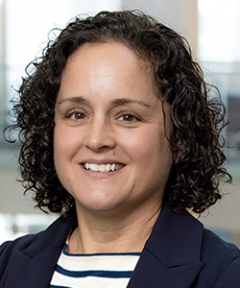
By Liz Beaulieu, Editor
Updated Tue February 14, 2012
A manual wheelchair that can be adjusted in less than one minute. A wheelchair battery panel that can be accessed without disassembly. A combined wheelchair motor and gearbox that comprises 7 SKUs instead of 80.
These are all improvements that Sunrise Medical, Pride Mobility Products and Invacare, respectively, have made to their wheelchair designs recently. Why? To make them easier and cheaper for providers and clinicians to service and maintain.
“In this environment, the lifecycle cost of the product is almost more important than the actual acquisition cost,” said Brian Ellacott, vice president and general manager of Invacare North American Commercial Operations. “Serviceability is key.”
With reduced reimbursement and with service calls costing anywhere from $80 to $200 a pop, according to estimates, it's no wonder providers and clinicians, and as a result manufacturers, want to make these visits infrequent, and when they do occur, fast.
Manufacturers are also making their wheelchairs easier and cheaper to service by incorporating common parts across product lines; and designing products that, when they do need to be repaired, require the use of few tools, they say.
“We spend considerable time with techs and ATPs, and in rehab facilities to find out what the pain points are,” said Brent Hatch, director of product management, adult manual, for Sunrise Medical.
For wheelchairs that are more complex, manufacturers are even trying to design products that can be repaired with end users still sitting in them, they say.
“They don't have to take the positioning system off and they don't have to get a person who's in a chair all day out of that chair,” said Ted Raquet, senior vice president of domestic sales for Pride Mobility Products.
Comments